Demolishing a building isn’t as simple as knocking down walls and clearing debris. In fact,…
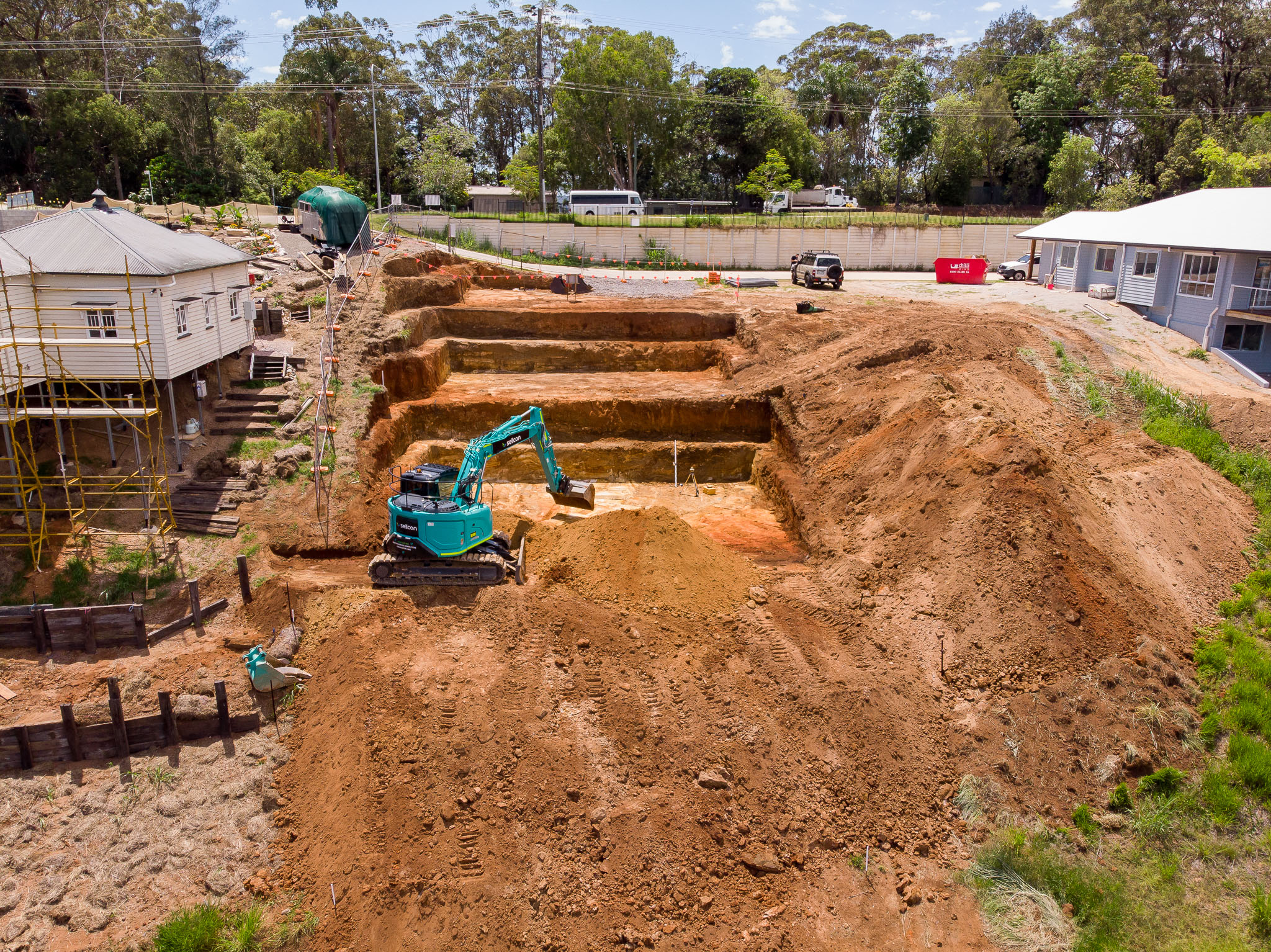
What to Expect During the Demolition Process & How to Prepare
Demolition can sound like a relatively straightforward job. And, in many ways, it is. And while the act of breaking down a structure is definitely part of the process, there’s a lot more happening behind the scenes.
Every structure is different. Some buildings may be old and unstable; others might be tightly packed between neighbouring properties. There could be hazards or challenges beneath the surface. That’s why precise planning is essential to ensuring the process is safe, efficient, and compliant. From site assessments and permits to hazard management and equipment selection, it all needs to be carefully considered before the first wall comes down.
At Sellcon, we know this process can be complex and overwhelming. However, a basic understanding of what to expect and how to prepare can make the experience a lot smoother. By knowing the key stages, requirements, and potential challenges ahead of time, you’ll be better equipped to make informed decisions and avoid unnecessary delays or complications.
Understanding the Demolition Process
When you think of demolition, you might think – knock it down, clear it out, job done. But in reality, demolition is a highly complex and precise process that plays a crucial role in the broader world of construction, redevelopment, and land use planning.
What Is Demolition, Really?
Demolition is the controlled dismantling, removal, or destruction of a structure, such as a house, whether that’s a house, a commercial building, or part of an infrastructure project. This shouldn’t be confused with deconstruction, where various materials are salvaged for future use.
It is also important to consider what demolition doesn’t include, which is the taking down of temporary construction supports like scaffolding or removing utility poles. Proper demolition is about safely and efficiently removing structures through methods that have been planned well in advance.
These may seem like small distinctions, but are important when it comes to permits and compliance.
Why Demolish a Building?
Buildings don’t come down without good reason. In many areas, we are seeing buildings reaching the end of their useful life or no longer serving their purpose. In fact, many buildings reach the end of their useful life after 80 to 100 years.
At that point, ongoing repairs, safety concerns, and changing land use make demolition a logical next step. Understanding this helps property owners make informed decisions about their next steps, whether that’s rebuilding, redeveloping, or simply clearing the way for something new.
Demolition usually happens when:
- Safety is a concern: Structural issues, unstable foundations, or damage from pests or natural disasters can make a building unsafe to occupy.
- Redevelopment is needed: As cities grow, older buildings often make way for newer developments or infrastructure upgrades. This is common across the Sunshine Coast and beyond.
- Extensive damage has occurred: Fires, floods, or cyclones can leave buildings beyond repair, making demolition the most practical solution.
- Hazardous materials are present: Older buildings may contain asbestos, lead paint, or other dangerous substances. Controlled demolition ensures safe removal.
- It’s more cost-effective: Sometimes it simply makes better financial sense to knock down an old structure and rebuild from scratch rather than investing in costly repairs.
- Land use has changed: As community needs shift, buildings may no longer serve their original purpose and need to be removed to make way for something new.
Different Types of Demolition Methods
Depending on the size of the structure, its purpose, and the reasons behind the demolition, the approach can vary significantly. In many cases, a combination of methods and techniques may be used to complete the project :
Residential vs Commercial Demolition
When it comes to demolition, not every job involves the same scale or approach. Residential and commercial demolitions are vastly different, both in size and complexity.
Residential demolition typically involves homes, units, or apartments. These projects are generally quicker, often completed within a few days, and usually don’t require the massive equipment and extended timelines that commercial demolitions demand. When it comes to a house knockdown, it’s more straightforward, though you’ll still need to consider things like nearby structures and the impact on surrounding properties.
On the other hand, commercial demolition involves larger buildings like office blocks, factories, warehouses, or shopping centres. These projects often take weeks or even months to complete, and they tend to be much more complex. The equipment used might be similar to residential demolition, but it’s usually scaled up to handle the larger structures.
Key differences include:
- Commercial buildings often have more intricate systems, like extensive HVAC networks, complex plumbing, and electrical systems, that need to be handled carefully.
- Residential demolitions require more attention to the surrounding environment, such as noise control and the proximity of neighbours.
- Commercial projects are often subject to stricter environmental and hazardous material regulations, such as managing asbestos or ensuring minimal disruption to nearby businesses.
Full vs Partial Demolition
Complete demolition means taking everything down, no walls are left standing. This approach is typically used when:
- The building’s structural integrity has been compromised.
- Repair costs would exceed the building’s value.
- You’re planning a completely new construction on the site.
Partial demolition, however, is more targeted and precise. In this approach, only certain sections of the building are demolished while the rest remains intact. This method requires meticulous planning and more careful execution. Partial demolition is used for situations like:
- Removing an outdated extension to make room for something modern.
- Knocking out interior walls to open up a space.
- Doing a remodel, like upgrading a kitchen or bathroom, while keeping the rest of the property intact.
- Removing damaged areas while preserving the structural integrity of the remaining sections.
Manual vs Mechanical Demolition
Manual demolition puts the power of skilled workers and tools like sledgehammers, jackhammers, and picks to work. This method is more labour-intensive but allows for more control and precision. It’s particularly useful in:
- Tight spaces where large machinery can’t access.
- Selective demolition, like removing specific walls or areas.
- Situations where materials need to be salvaged.
Mechanical demolition involves heavy machinery such as excavators, bulldozers, cranes, and occasionally the dramatic wrecking ball. This approach is faster and more efficient, especially for larger structures. It is also “safer”, as it keeps workers further from potential hazards, like falling debris. This method is often used for the bulk of demolition, with manual techniques taking over for the more delicate tasks.
Planning the Demolition
Proper demolition planning isn’t just good practice, it is a non-negotiable when it comes to the demolition process.
1. Conducting a Site Assessment
Every demolition plan starts with a full site assessment. Professional consultants get into the structure and surrounding areas to identify several potential risks such as:
- Fire or explosion risks
- Toxic or hazardous chemicals
- Asbestos or lead-containing materials
- Structural complexities that affect demolition methods
A qualified surveyor will assess the building’s structural integrity and check for faults and poor design that could impact the structure’s behaviour during demolition. More importantly, site assessments help identify risk factors to the project and surrounding areas, including traffic access needs.
Learn More: The Difference Between Friable & Non-Friable Asbestos
2. Permits and Approvals
You cannot legally start demolition work without the proper permits. In most cases, demolition approval is issued by your local council or a relevant building authority. This certifier will review your plans, ensure they comply with applicable codes and legislation, and confirm that the proposed work meets safety and structural standards.
However, the specific requirements and related fees can vary depending on the location, type of structure, size and scope of the work, and current legislation.
An application typically covers:
- Detailed site plans showing structures to be removed
- Proof of utility disconnections
- Asbestos assessment documentation
If you are unsure what you need, contact your local council to understand your area’s specific requirements or consult with a qualified building surveyor or private certifier who will guide you through the approval process and help avoid costly missteps
3. Hiring Licensed Demolition Contractors
The right demolition contractor can make all the difference in your project’s success. A licenced demolition contractor is required for structures over 4 meters in height or with load-bearing elements.
Here’s what to check before signing anyone on:
- Are they licensed? (Look for a DE1 or DE2 license depending on the height of the structure)
- Do they have valid insurance and public liability coverage?
- Can they show experience with similar jobs?
- Do they have a strong safety record and documented safety plans?
Professional demolition contractors protect you from potential fines and make sure all documentation requirements are properly handled. They create detailed demolition plans that outline methodologies and procedures needed for project safety and success.
Legal & Safety Considerations
Beyond securing the necessary permits and approvals, there are strict safety measures and legal obligations that must be followed to protect workers, neighbours, and the environment. Here’s what needs to be considered:
Hazardous Material Identification & Removal
If you’re dealing with a building constructed before the 1990s, there is a good chance you’ll be dealing with hazardous materials. An assessment is essential before any demolition begins. This survey checks for:
- Asbestos: Found in everything from roof sheeting to old vinyl flooring.
- Lead-based paint: Common in homes built before the 1970s.
- Polychlorinated biphenyls (PCBs) and other chemical hazards: Found in older electrical equipment or sealants.
Asbestos removal is not DIY job. It must be handled by licenced professionals trained to contain and safely dispose of it. Exposure to asbestos fibres and dust from lead paint can lead to life-threatening conditions.
Safety for Neighbours, Pedestrians & Surrounding Properties
Demolition doesn’t happen in isolation, it also impacts the people, properties, and environment around them. Proper planning is needed to ensure the safety of everyone nearby. This includes:
- Secure fencing and perimeters: Erecting sturdy, tamper-proof fencing is one of the first steps on any site. It prevents unauthorised access, protects curious bystanders, and creates a clearly defined exclusion zone around hazardous areas. Signage should also be placed around the perimeter to warn of dangers and guide workers and visitors safely.
- Environmental impact assessments: Before demolition begins, an Environmental Impact Assessment (EIA) may be required, especially for large or sensitive sites. This assessment identifies potential risks to air quality, soil health, and nearby water sources and recommends strategies to reduce environmental harm. Proper waste disposal, hazardous material handling, and pollution prevention methods are all guided by this assessment.
- Noise and dust control measures: Demolition can be noisy and dusty, especially in densely populated or residential areas. To minimise the impact, measures may include using noise barriers, dust suppressants, specific working times and more.
- Communication with neighbours and stakeholders: Letting neighbours know what to expect, when demolition will take place, and how any disruptions will be managed can go a long way in building trust and avoiding complaints. Notices, letterbox drops, and even local information sessions may be appropriate for larger jobs.
Safe Work Method Statements (SWMS)
Every demolition project, no matter the size, must be backed by a Safe Work Method Statement (SWMS). A SWMS outlines how demolition work will be carried out safely and systematically, helping to prevent injuries, manage risks, and ensure compliance. It must be prepared before work begins, made easily accessible on site, and reviewed regularly as the project progresses or conditions change.
Your SWMS must clearly cover:
- Identified hazards and associated risks: This includes everything from falling debris, structural instability, and hazardous materials to working at heights, noise exposure, and nearby utilities (like gas and power lines). Each hazard is assessed for its potential impact and likelihood.
- Steps to control those risks: Once risks are identified, the SWMS details exactly what measures will be put in place to minimise or eliminate them. These can include temporary structural supports, exclusion zones, personal protective equipment (PPE), specialised machinery, or the sequencing of tasks to avoid unnecessary exposure.
- Safe work practices and procedures: This section describes how the demolition will be done safely. It outlines who is responsible for each task, the tools and equipment to be used, and specific instructions for high-risk activities. It also covers training requirements, communication protocols, and supervision standards.
- Emergency procedures: If something goes wrong, the SWMS acts as a first-response guide. It must include clear instructions for evacuation, injury management, incident reporting, and contacting emergency services. Everyone on site should be briefed on these procedures before work begins.
Pre-Demolition Checklist
Proper planning and preparation are critical to the success of any demolition project. Addressing the following areas in advance will help mitigate risk, ensure compliance with legal and safety standards, and may provide opportunities to reduce costs through material recovery.
1. Disconnecting Utilities
Before demolition can proceed, utility services must be safely and completely disconnected by licensed professionals. It is important to distinguish between disconnection (temporary service suspension) and abolishment (complete removal of infrastructure such as meters and cables).
For electricity, the abolishment process typically involves:
- Contacting the electricity retailer (the company that issues electricity bills)
- Requesting a formal abolishment service order
- Notifying the demolition contractor of the upcoming abolishment
- Allowing the network provider to assess site requirements
- Confirming the abolishment date once scheduled
The following services must be disconnected as we;;:
- Electricity
- Gas
- Water and sewerage
- Stormwater drainage
- Telephone lines, internet, and NBN
Failure to disconnect utilities properly can lead to major safety risks, including gas leaks, electrocution, or flooding.
2. Salvaging Valuable Materials
Before demolition, there is the opportunity to recover valuable building materials that may otherwise be discarded. These can be sold, donated or recycled. Materials worth salvaging include:
- Kitchens, bathrooms, and laundries, especially full suites in good condition
- Hot water systems, lighting fixtures, windows, doors, and hardware
- Timber flooring, vintage carpets, feature tiles, and heritage architectural details
- High-value items like chandeliers, fireplace mantels, or brass fittings
3. Informing Neighbours and Managing Expectations
Clear and early communication with neighbours helps avoid complaints, builds goodwill, and ensures everyone’s on the same page. Provide written notice at least 5–10 business days before work begins and should include:
- Start and expected end dates of demolition
- Working hours and days contractors will be on site
- Notice of heavy equipment arrival or street disruptions
- Your contact details and your demolition contractor’s information
This communication should also address key concerns such as site safety, noise, dust management, and hazardous material handling. Transparency in the planning stage supports a smoother and more cooperative process.
The Demolition Process
Once all pre-demolition requirements are fulfilled, demolition can begin. Each stage is carefully planned to ensure everything runs smoothly, safely, and with as little impact on the environment as possible.
1. Setting Up the Site and Safety Measures
The first step is securing the area. Temporary fencing, warning signs, and clear exclusion zones (usually at least 5 metres) are set up to keep people safe and away from the demolition zone. Contractors check that all hazardous materials have been removed, and install dust control systems if needed. A final walkthrough ensures everything is ready before any heavy machinery arrives.
2. Tools and Machinery
Different buildings call for different tools and techniques. Most residential demolitions use excavators with special attachments to break things down, along with bulldozers and loaders to move debris.
Bigger or more complex sites might need equipment like hydraulic shears to cut steel. Hand tools like sledgehammers and jackhammers are used when more precision is needed, especially around tight spaces or delicate features.
3. The Demolition Process Step by Step
Demolition usually follows a top-down approach to keep things stable and safe. Here’s a typical sequence:
- Remove fittings and internal features (like kitchen cabinets, lights, etc.)
- Strip off roofing materials
- Carefully take down walls, one floor at a time
- Remove structural supports with caution
- Break up the foundation and concrete slabs last
4. Clearing the Debris and Managing Waste
As the building comes down, debris is removed in stages using loaders and trucks. Waste is sorted and placed in temporary holding areas before being taken off-site. All this is done under strict guidelines to make sure disposal is legal, safe, and responsible.
Not everything from a demolition site goes to landfill. Materials like concrete, metal, timber, and bricks can be sorted and either recycled on-site or sent to specialised facilities. Tools like magnets help pull out metals, while other systems help sort wood, plastics, and other materials. Recycling reduces waste and gives old materials a second life.
5. Final Site Inspection and Sign-Off
Once the demolition is complete and the site has been cleared, a final inspection is carried out. This includes checking for any damage to nearby properties and making sure all safety and environmental standards have been met. Once everything’s approved, you’ll receive clearance, and your site will be ready for the next phase of development or construction.
Key Takeaways
Demolition projects involve more complexity than meets the eye. Clear, comprehensive, and proper planning is the foundation of even the smallest demolition project. Without thorough preparation, risks increase, delays can occur, and the entire process may become far more costly and time-consuming than necessary. By carefully considering every detail, from securing permits to waste management and safety protocols, you ensure a smoother and more efficient demolition experience.
At Sellcon, we understand the complexity that comes with demolition and approach every project with the utmost care and precision. Whether you’re tackling a residential or commercial demolition, our team combines time-tested techniques with the latest equipment to deliver reliable results.
We work closely with you every step of the way, ensuring your project is completed on time, within budget, and with minimal disruption. Get in touch today to learn more.