Partial demolition sounds simple. After all, you're only removing part of the structure, right? However,…
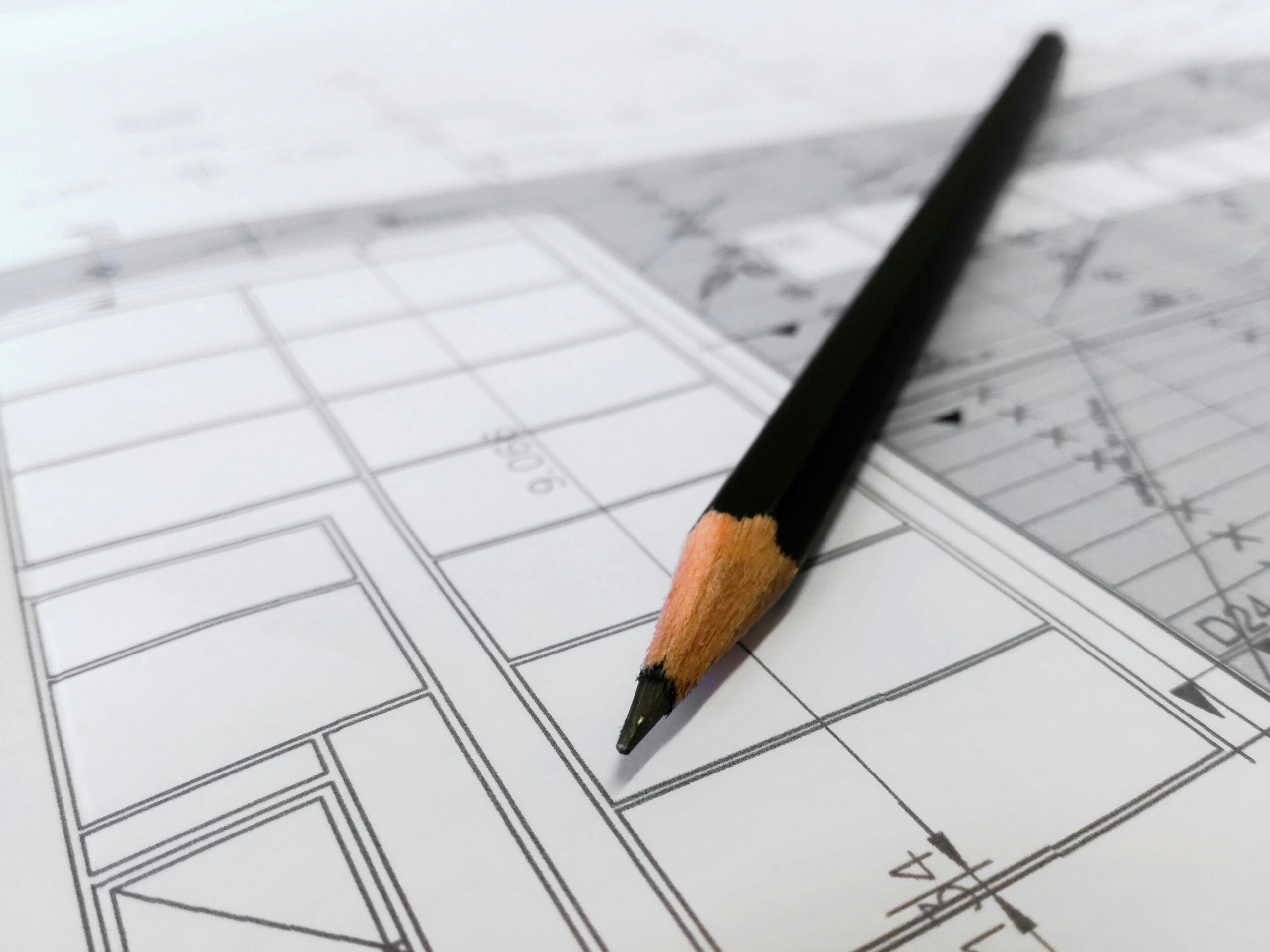
What Is A Demolition Plan?
Demolishing a building isn’t as simple as knocking down walls and clearing debris. In fact, it’s a highly complex process that carries significant risks and financial consequences if not performed correctly. This is why demolition requires careful planning, specialised equipment, and strict safety measures. For tall buildings or structures that require specialised machinery, a detailed plan becomes even more critical.
A well-structured Demolition Work Plan (DWP) is the foundation of any successful building removal project. It is a document that outlines every step of the process, ensuring that demolition is carried out efficiently, safely, and in compliance with relevant regulations.
While the nature of individual demolition plans will depend on the complexity of the project and local restrictions and laws. In this post, we cover everything you need to know about demolition plans – from what they are to key components that should be considered and included when developing a Demolition Work Plan (DWP).
What Is A Demolition Work Plan?
By definition a demolition work plan is a structured document that outlines the various steps and considerations of a demolition project. It includes the method of demolition, safety procedures and risk assessments, waste management strategies, environmental considerations and necessary permits required to safely and efficiently demolish a structure.
Key Elements Of A DWP
- Identifies Elements to Remove: A demolition plan specifies exactly which parts of the structure need to be dismantled, demolished or removed. This includes structural elements, interior finishes, vegetation, exterior finishes and more. This ensures that no part of the structure is overlooked and that any hazardous materials are properly managed.
- Details Demolition Method: A demolition work plan outlines the chosen demolition method based on the building’s structure and site conditions. Whether it’s controlled collapse, mechanical dismantling, or explosive demolition, the plan ensures that the most suitable and safest approach is selected for the project.
- Safety Considerations: Safety is essential in any demolition project. The demolition work plan details the safety measures in place to protect workers, the surrounding area, and the public. This includes establishing exclusion zones, managing debris effectively, and specifying the personal protective equipment (PPE) required for everyone on site.
- Environmental Impact Assessment: The plan addresses the environmental concerns associated with demolition, such as dust control, asbestos management, and waste disposal. It ensures that the project complies with environmental regulations, minimising the impact on the surrounding area and local communities.
- Permits and Approvals: Before any demolition work begins, the demolition work plan outlines the permits and approvals required from local authorities. This ensures that the project is legally compliant and adheres to local building codes and regulations.
Types Of Demolition Methods
The primary goal of demolition is to clear a site quickly and efficiently, but the method used depends on factors such as the structure’s size, location, materials, and environmental considerations. There are three primary methods of demolition: manual, mechanical and explosive.
Mechanical Demolition
Mechanical demolition is the most common method of tearing down buildings. It involves the use of heavy machinery, such as hydraulic excavators, bulldozers, and wrecking balls, to systematically dismantle a structure.
It is best used for medium to large-sized buildings or buildings used in urban and industrial settings where controlled, systematic dismantling is necessary.
Benefits:
- Versatile and can be applied to most structures
- Safer than explosive demolition in many cases
- Allows for better management of debris and materials
Considerations:
- Slower than explosive demolition
- Requires efficient handling to ensure minimal disruption
- Not always suitable for tight spaces or highly congested areas
Explosive Demolition
Explosive demolition involves strategically placing explosives to bring down a structure in a controlled manner. This technique is often used for high-rise buildings, bridges, and industrial plants or for projects where speed and efficiency are a top priority.
Benefits:
- It is the fastest method and can bring down a structure in seconds
- It is efficient and requires less labour compared to deconstruction
- Safe when executed correctly as it minimises worker exposure to hazardous conditions
Considerations:
- Planning and explosives make it an expensive option
- Requires structural analysis to ensure feasibility, so it is not suitable for all buildings
- Generates a significant amount of noise, dust, and vibration, requiring extensive safety precautions
Deconstruction (Manual Demolition)
Deconstruction refers to the manual disassembly of a structure. Instead of quickly tearing down a structure, it is dismantled piece by piece to salvage valuable materials such as wood, metal, and bricks. This allows for the reuse and recycling of materials, making it the most environmentally friendly demolition method.
This is the preferred method for historical or heritage buildings where preservation is important or smaller structures or areas with limited space where heavy machinery cannot operate.
Benefits:
- Reducing waste and allowing for material reuse
- Ideal for recycling or preservation as it keeps valuable building materials in circulation
- Generates minimal dust, noise, and vibration compared to mechanical or explosive demolition
Considerations:
- Extremely labour-intensive and time-consuming. Depending on the structure, it can take weeks or months compared to other methods
- Specialised knowledge is needed to dismantle structures safely
- The labour and time investment make it more expensive than other demolition methods
Pre-Demolition Considerations
Demolition work refers to activities involved in demolishing, deconstructing, or dismantling a structure (or part of a structure) that is load-bearing or important to the physical integrity of the building. However, this does not include activities such as dismantling formwork or removing power poles.
Before any demolition work begins, there are several key factors that consider and taken into account. These factors will be included in the Demolition Work Plan (DWP), ensuring that all aspects of the project are carefully planned and potential risks are mitigated. These considerations typically include:
Obtaining Permits & Approvals
If you are looking to demolish a structure, it is essential to ensure you have all the necessary permits and approvals from local regulations and councils. Demolition work is highly regulated to protect public safety, the environment, and surrounding structures, so failing to obtain the correct permits can result in delays, fines, and even legal consequences. Key considerations include:
- Demolition Work Licence: A person conducting a business or undertaking (PCBU) must hold a valid demolition work licence to carry out demolition activities. This ensures that the company has met safety standards and is legally allowed to operate on demolition projects.
- Nominated Competent Person: Under the demolition licence, a competent person must be nominated to supervise the work. This person is required to be readily available to supervise workers, ensuring safety and regulatory compliance throughout the process.
- Worker Training: The PCBU must provide appropriate training for all workers involved in the demolition. This training ensures that workers are equipped with the necessary skills and knowledge to carry out the work safely and competently.
- Construction Work Regulations: Demolition is considered part of construction work and must adhere to relevant construction regulations, including those related to worker safety and structural integrity.
- Safe Work Method Statements (SWMS): High-risk demolition activities, such as demolishing load-bearing structures, require detailed safe work method statements. These statements outline safety procedures to ensure the work is carried out without incident.
- Notification of Demolition Work: At least five days before starting demolition, Workplace Health and Safety Queensland must be notified if the project involves certain high-risk factors, such as demolition of a structure or part of a structure that is at least 6 meters in height, use of load-shifting machinery on a suspended floor, use of explosives during demolition.
- Asbestos Considerations: When demolishing structures containing asbestos, additional steps and considerations must be taken. Asbestos removal requires specialist knowledge and specific permits to prevent exposure to harmful materials.
- Notifiable Incidents: If a structure collapses or partially collapses during demolition, it constitutes a dangerous incident. This must be reported to Workplace Health and Safety Queensland immediately.
While the permit and approval process may seem overwhelming, a demolition work plan will outline all the necessary permits and approvals that will be needed. Professional demolition services can help navigate the complexities of compliance and help ensure that all permits and approvals are in place before beginning the demolition work.
With in-depth knowledge of the regulatory requirements and years of experience, they can navigate the complexities of the process with ease, ensuring your project stays compliant, on track, and free from costly delays.
Conducting Structural & Site Surveys
While the structure is set to come down, it is still essential to have a full understanding of both the structure and site conditions. This helps to identify potential risks and challenges that may occur during demolition.
A qualified surveyor should handle the structural investigation, especially for partial demolitions. The structural survey examines the building’s overall integrity, identifies any faults or design weaknesses, and pinpoints any temporary work required for safe demolition. Some of the key factors covered in the structural survey include:
- Age of the Structure: Older buildings may have deteriorated materials or outdated construction methods that require extra attention or special handling during demolition.
- Previous Use: The building’s prior use may impact the demolition process, especially if it involved hazardous materials or unique features that need to be addressed (e.g., industrial buildings, schools, or medical facilities).
- Type of Construction: Different types of buildings require different approaches. Whether the building is made of steel, concrete, or timber will dictate the most effective demolition methods.
- Nearby Buildings or Structures: A structural survey will consider adjacent buildings or structures that might be affected by the demolition, preventing any damage during the process.
A site appraisal must also be conducted to evaluate the surrounding environment and existing site features. A site appraisal should cover:
- Protection Levels for the Public: Ensuring that the public is protected from any potential hazards by setting up exclusion zones and other safety measures.
- Access Limits on Plant Size and Equipment: Identifying any site access restrictions, such as narrow lanes or limited space, that could affect the size of equipment and machinery used during demolition.
- Possible Site Contamination: Identifying any contaminants, such as asbestos or hazardous chemicals, that may be present on the site, as well as any potential ground subsidence issues.
Hazardous Materials Assessment
Identifying and managing hazardous materials are one of the most important steps in a demolition work plan. Many construction products used before the 1980s likely contain harmful substances like asbestos, lead-based paint, polychlorinated biphenyls (PCBs), and synthetic mineral fibres, which are hazardous to human health and the environment if not handled properly.
A thorough hazardous materials assessment ensures that these dangerous substances are identified and removed (if required) before any demolition work begins. You must get a copy of the workplace’s asbestos register before starting any demolition. If no register exists, a qualified person needs to check the structure for asbestos or asbestos-containing materials (ACM)
This involves sampling materials from the structure and sending them to certified labs for testing. Once hazardous materials are identified, the demolition plan must outline specific procedures for safely removing, handling, and disposing of these materials in compliance with environmental regulations.
Planning for Noise, Dust, & Debris Control
Noise, dust, and debris not only affect the health and safety of workers but also the surrounding community and environment, so addressing these are essential.
Noise Control
Demolition work is often noisy, and to comply with local regulations and minimise disturbance to nearby residents and businesses, noise control is essential. Noise management plans should be developed in accordance with AS 2436 – Guide to Noise and Vibration Control on Construction, Demolition, and Maintenance Sites, which provides standards and guidelines for effective noise mitigation. Key strategies include:
- Creating a Noise Management Plan: This plan outlines measures to control excessive noise, ensuring that demolition work complies with noise limits set by local authorities.
- Scheduling Work Hours: Limiting demolition activities to acceptable hours, such as daytime work, can help reduce the impact of noise on surrounding areas.
- Using Sound Barriers: Where possible, setting up barriers or enclosures around the demolition site can help absorb and reduce the spread of noise.
Dust Control
Dust generated during demolition can pose significant health risks to workers and contribute to air pollution in the surrounding area. Proper dust control measures are crucial for maintaining a safe working environment and protecting the community. Some proven dust control methods include:
- Water Sprays and Dust Suppression: Using water sprays or dust suppression systems during demolition helps to settle dust and keep it from becoming airborne.
- Strategic Scheduling: By carefully scheduling demolition work, especially when disturbing large areas of earth, dust can be minimised. Timing the work to avoid windy conditions further reduces dust exposure.
- Keeping Surfaces Moist: Keeping disturbed surfaces moist until vegetation regrows or the site is stabilised can significantly reduce dust generation.
- Windbreaks: Installing windbreaks, such as fences or temporary barriers, helps reduce the movement of dust, especially in open or windy areas.
Debris Control
A debris management plan ensures that materials are safely removed and disposed of, reducing hazards on-site and minimising environmental impact. Some best practices include:
- Waste Management Plan: A comprehensive plan for managing materials on-site should include details on how debris will be sorted, handled, and disposed of, with a focus on reuse and recycling where possible.
- Containment: Ensuring that debris is kept within the site boundaries and that appropriate containers or barriers are used to contain materials will prevent accidental dispersal.
- Timely Removal: Regularly removing debris from the site helps to maintain a safe and organised workspace while minimising the potential for accidents.
Utility Disconnections & Site Preparation
Site preparation and utility disconnection are one of the final pre-demolition steps and should be outlined in the demolition plan to ensure that all essential services are safely terminated and the site is properly prepared for the demolition process. Utility disconnections should cover all essential services, including electricity, gas, water, sewerage, and telecommunications.
- Electricity: Your electricity retailer must permanently remove the network connection. Demolition can’t start without written confirmation.
- Gas: All gas lines need to be disconnected, and some pipes must be removed.
- Water: You might need meter removal and underground pipe work. Water should be capped at the street.
- Sewerage: A qualified plumber usually handles this. Special installations like composting systems might need specific removal advice.
- Telecommunications: Your provider will guide you through disconnecting phone lines, internet, and NBN services.
Additionally, comprehensive site preparation ensures that the demolition area is clear of obstacles, secure from public access, and ready for the equipment and machinery necessary for the job. This includes setting up exclusion zones, establishing safe access points, and ensuring all non-structural elements are removed.
Steps To Creating A Demolition Plan
A demolition plan requires careful attention to detail and organised components to ensure a safe, quick, and compliant project outcome. Below are some key steps in creating a demolition plan:
- Assessing the Project Scope and Objectives: This includes identifying what needs to be demolished, understanding the site conditions, and determining potential challenges like access routes. This assessment ensures clear project boundaries and helps plan resource allocation effectively.
- Selecting the Appropriate Demolition Method: Choosing the right demolition method depends on the size, location, and materials of the structure. Mechanical demolition is typically the most cost-effective for standard projects, but other methods like explosive demolition may be necessary for complex structures.
- Creating a Safety and Emergency Response Plan: Safety is essential in demolition, and having a comprehensive plan in place is crucial. This includes having a trained emergency response team, proper containment systems for hazardous materials, and clear incident response protocols.
- Developing a Waste Management and Recycling Strategy: Efficient waste management reduces costs and environmental impact. Set up waste sorting procedures, partner with recycling facilities, and reuse materials like concrete on-site. This strategy helps minimise landfill waste and supports sustainability goals.
- Timeline and Cost Estimation: Accurate time and cost projections are key to a successful project. Consider factors like structure complexity, hazardous materials, and disposal logistics when creating your timeline.
- Safety & Environmental Considerations: Prioritise both worker safety and environmental protection by implementing proper PPE, dust control, and debris containment measures. Workers should have specialised training in hazard identification. These protocols minimise risks and help ensure compliance with health and environmental standards.
- Hazard Identification and Mitigation Strategies: Identify potential hazards early through a detailed risk assessment. This allows for the implementation of control measures such as hazard elimination or substitution, along with proper PPE. Effective mitigation strategies protect both workers and property.
- Emergency Protocols and First-Aid Preparedness: Have clear emergency procedures in place, including evacuation plans, medical protocols, and accessible first-aid stations. Ensure there are enough trained first-aid officers on-site.
- Ensuring Public and Environmental Safety: Protect the public and environment by using dust control systems and debris barriers. It is also important to coordinate with local councils to minimise disruptions and take extra care if hazardous materials like asbestos are present. Proper handling ensures safety and minimises environmental impact.
Key Takeaways
Ultimately, demolition projects require careful planning, safety protocols, and the right expertise to ensure efficiency and success. By prioritising safety and preparation, you can protect workers, the public, and the environment while keeping your project on track.
At Sellcon, we never compromise on safety. With over 16 years of experience, we are your trusted demolition partner in Southeast Queensland and the Sunshine Coast. Whether it’s residential, commercial, or industrial demolition, we offer reliable, efficient, and high-quality solutions tailored to your needs.
Ready to get started? Contact Sellcon today for a free consultation, and let us help you with your next demolition project.