Demolition can sound like a relatively straightforward job. And, in many ways, it is. And…
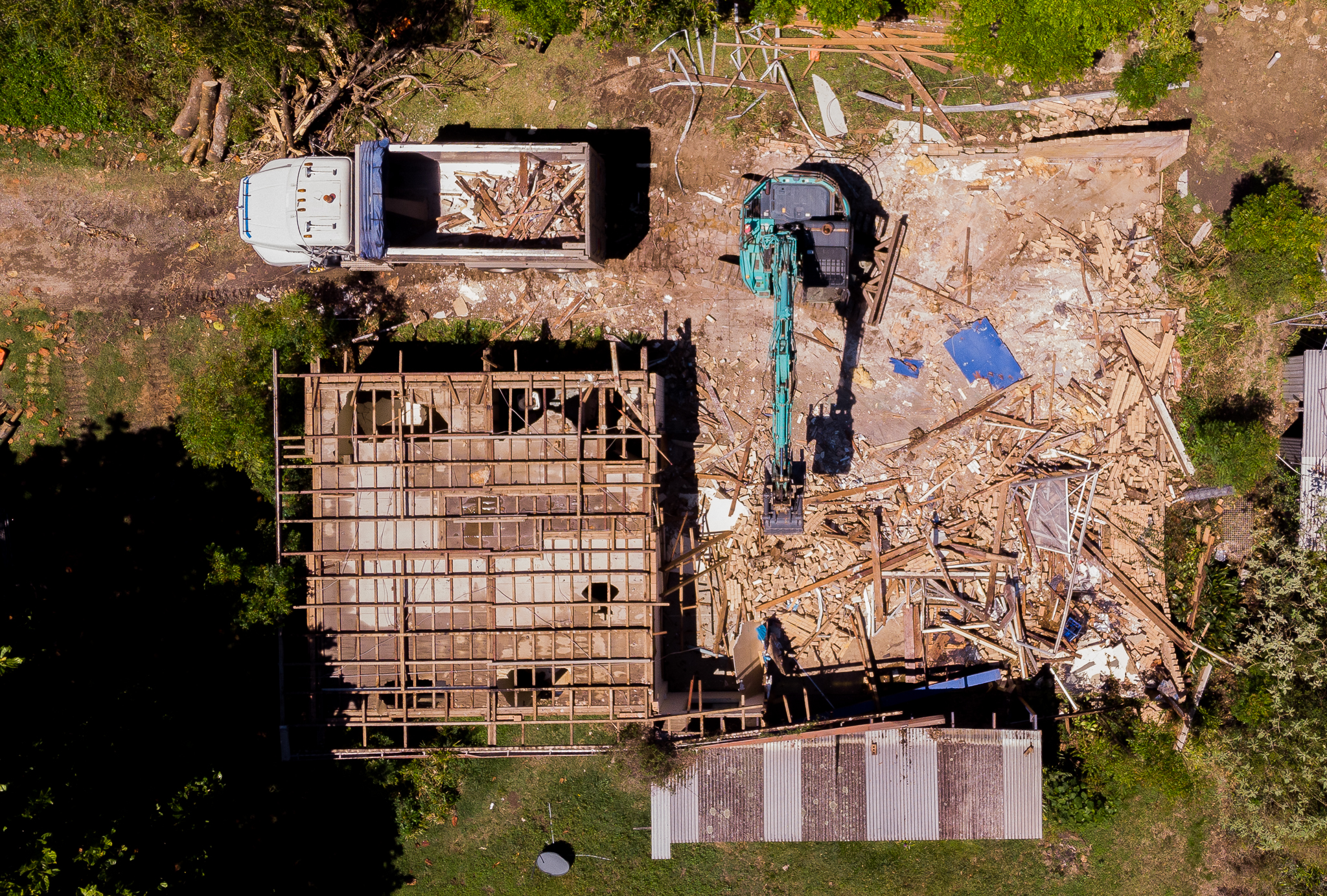
Partial Building Demolition: Methods, Challenges, and Solutions
Partial demolition sounds simple. After all, you’re only removing part of the structure, right? However, that assumption couldn’t be further from the truth.
Partial demolition actually presents some of the trickiest challenges in the demolition industry, requiring surgical precision, detailed planning, and specialised expertise that goes well beyond what you’d need for a complete teardown.
Yes, these jobs are typically smaller in scale, but unlike full demolition projects, where we can simply bring everything down, partial demolition means removing specific sections of a structure while keeping the rest standing and structurally sound. This means having the right plans and permissions in place. Cutting corners can lead to costly mistakes – or worse, unsafe conditions.
This selective approach becomes essential when you want to renovate rather than rebuild from scratch. Though we should mention upfront – depending on the damage and work involved, renovation isn’t always the cheaper option when compared to starting fresh.
Older homes also often hide unexpected and expensive surprises, so before you can even think about starting any partial demolition work, a thorough assessment of your existing structure is absolutely essential.
In this post, we cover everything you need to know about partial demolition, from the different methods used to the unique challenges they present and solutions to solve them.
What is Partial Demolition?
Partial demolition, also known as selective demolition, is the careful and controlled removal of specific parts of a building while preserving the rest of the structure. Unlike full demolition, where the entire building is taken down, partial demolition focuses on targeting certain elements, such as a wall, a room, or even a section of a roof, without compromising the structural integrity of what remains.
This process is often used in both residential and commercial projects to allow for renovations, extensions, or updates without starting from scratch. In homes, partial demolition might be used to:
- Open up living spaces by removing dividing walls
- Add new extensions by taking down exterior sections
- Update areas to meet modern building codes
- Replace outdated or faulty plumbing systems
- Remove old features like fireplaces or chimneys
In commercial settings, it plays a key role in:
- Reconfiguring interiors for better layouts
- Retaining historical facades during modern upgrades
- Modifying load-bearing structures like beams or columns
- Replacing or upgrading roofs, staircases, and elevators
One of the main challenges of partial demolition is that it requires extreme precision. Workers need a thorough understanding of the building’s components, including structural, plumbing, electrical, and cable systems to avoid causing unintended damage. Often, small-scale machinery and manual tools are used to ensure targeted removal with minimal disruption.
Common Methods Used in Partial Demolition
So, you’ve completed the assessments and ticked off the paperwork, now it’s time to talk about how the work gets done.
Partial demolition isn’t a one-size-fits-all process. Different projects call for different approaches, and the tools we use depend entirely on what you’re trying to achieve. Let’s break down the main methods we use for partial demolition work.
1. Manual Demolition Techniques
Manual demolition involves breaking down parts of a structure using hand-operated tools rather than heavy machinery. This method is ideal for jobs that require surgical precision or are located in tight spaces where larger equipment simply can’t access.
Common tools used include:
- Hammers and chisels
- Crowbars and pry bars
- Sledgehammers for extra impact and control
The process typically starts with removing non-structural elements like fixtures, finishes, and drywall, before carefully dismantling structural components from top to bottom.
Why choose manual demolition?
- Greater precision to preserve specific parts of the building
- Lower risk of disturbing hazardous materials like asbestos
- Minimal noise and vibration — great for sensitive sites
- Higher potential for salvaging reusable or recyclable materials
2. Mechanical Demolition Tools
For larger-scale or more complex projects, mechanical demolition is often the go-to approach. It uses powerful machines equipped with specialised attachments to remove parts of a structure quickly and efficiently.
Key machinery includes:
- Excavators
- High-reach excavators
- Skid steer loaders
Mechanical demolition speeds up the process while still allowing a high degree of control.
3. Selective Deconstruction
Considered “construction in reverse,” selective deconstruction focuses on taking apart building components you can reuse, repurpose, or recycle. Everything starts with a detailed inventory to find valuable materials like hardwoods, architectural features, or historic bricks.
- Hardwood flooring
- Decorative trim and fittings
- Architectural features
- Historic bricks and timbers
Crews then work in stages, removing interior finishes first, followed by structural components. Materials are sorted on-site, reducing waste and landfill impact. In many cases, salvaged items can even be resold, helping offset project costs.
Benefits of selective deconstruction:
- Supports sustainable building practices
- Creates less dust and disruption
- Allows recovery of high-value materials
- Reduces environmental impact significantly
Key Challenges in Partial Demolition Projects
Due to the nature of partial demolition projects, there are technical challenges that need to be considered. The most common include:
Structural Stability And Load-Bearing Concerns
Building collapse is the main risk in partial demolition. Safety regulations classify load-bearing element demolition as “high-risk construction work”.
A full assessment of the structure must come first. The work needs building approval, licensed builders, and sometimes structural engineers. This means a Safe Work Method Statement (SWMS) is required before work starts.
Engineers need to review materials, load-bearing walls, and overall integrity to find the quickest way to demolish safely. Taking out a load-bearing wall without proper support leads to sagging roofs, uneven floors, cracked walls, and maybe even complete collapse. Teams often use temporary braces to keep structures stable throughout the process.
Managing Dust, Noise, And Debris
Dust creates serious health risks during demolition. Workers face respiratory problems and skin irritation while nearby areas suffer from poor air quality. Several strategies are used to keep dust under control: water sprays or misting systems to suppress airborne particles, chemical dust suppressants, enclosed demolition techniques, and regular air quality monitoring.
Excessive dust on job sites doesn’t just threaten worker health – it can also:
- Speed up engine wear on equipment, bumping up maintenance costs
- Spread beyond the site boundaries, creating problems with neighbours
- Lead to regulatory violations, since many Queensland councils have specific dust control requirements
Proper debris management is equally critical for safety and environmental protection. Uncontrolled debris can cause accidents, environmental contamination, and regulatory breaches. We implement waste segregation right at the source and provide adequate containers for different waste types to prevent cross-contamination and simplify transport.
Beyond dust and debris, working in a confined demolition puts workers at risk. Hazards include:
- Loss of consciousness
- Injury, or death from contaminants
- Fire
- Explosion
- Oxygen deficiency
Thus, these spaces need written risk assessments from experts, entry permits, warning signs, and emergency procedures.
Unexpected material issues like asbestos
Many older homes built before 1990 used hazardous materials like lead-based paints and asbestos-containing products in their construction. In fact, it is said that one-third of Australian homes contain asbestos products.
Today, asbestos is one of the most tightly regulated hazardous materials in the construction and demolition industry. Even minor disturbances to asbestos-containing materials (ACMs) can release dangerous fibres into the air, posing serious health risks such as mesothelioma and asbestosis.
If your partial demolition project involves an older structure, it’s essential to:
- Conduct a professional asbestos inspection before any work begins
- Arrange for licensed asbestos removal if it’s detected
- Ensure all works comply with Safe Work Australia guidelines and local regulations
Failing to properly identify and manage asbestos can lead to hefty fines, project delays, and major safety concerns. It’s one of the most common (and costly) surprises in older home renovations, so identifying it early is key to staying on schedule
Solutions and Best Practices for Success
When it comes to partial demolition, proper preparation and smart execution make all the difference. Projects that run smoothly are the ones where every detail is carefully sorted before the first tool even touches the building. Here’s how to set your demolition up for success:
Detailed Structural Assessments
Thorough planning and deep structural assessment are the foundation of any successful partial demolition project. A comprehensive site inspection helps identify hazards and informs the safest, most efficient approach before work begins.
Engineers will evaluate the building’s materials, load-bearing elements, and overall condition to develop a custom demolition plan that keeps the remaining structure stable and secure.
An assessment should cover:
- Identification of critical load-bearing structures
- Analysis of existing movement patterns within and around the site
- Evaluation of how neighbouring buildings and infrastructure might be affected
- Planning safe methods to remove targeted sections without compromising stability
These checks allow you to carefully map out the demolition process, reducing risks, avoiding costly delays, and protecting everyone on site. A full structural assessment not only safeguards the project but also speeds up completion by preventing unexpected setbacks.
Hiring Skilled Professionals
Partial demolition is complex, and having the right team ensures the best results. Experienced contractors bring knowledge that helps identify challenges early and develop effective solutions tailored to your project.
Sellcon has over 16 years of industry experience serving Southeast Queensland and the Sunshine Coast with high-quality, safe residential, commercial, and industrial demolition solutions.
We ensure:
- Compliance with safety and environmental regulations
- Efficient waste management and recycling
- Coordination with engineers, architects, and local authorities
Effective Stakeholder Communication
Clear, proactive communication is critical to the success of any partial demolition project, especially when it’s in a residential or busy commercial area.
Good community engagement involves:
- Informing neighbours, tenants, and employees about what to expect
- Providing advance notice of demolition timelines and potential disruptions
- Explaining how hazardous materials will be safely managed
- Offering opportunities for feedback and addressing concerns promptly
Maintaining open communication channels builds trust, reduces complaints, and creates a cooperative atmosphere throughout the project. When stakeholders feel heard and informed, demolition work proceeds more smoothly for everyone involved.
Legal, Safety, and Planning Considerations
When it comes to partial demolition in Queensland, the paperwork and permits can be just as complex as the physical work itself. Various legal frameworks govern everything from planning approvals to safety protocols, and understanding these requirements upfront will save you from delays, fines, and potential legal headaches down the track.
Does Partial Demolition Require Planning Permission?
The short answer? It depends on your location and project scope. Planning permission requirements for partial demolition vary significantly across Queensland councils, but there are some common triggers you need to know about.
You’ll typically need planning approval when you’re demolishing more than half the volume of a building, or when removing any façade facing a street that’s partly visible from that street. Heritage properties present their own challenges, and even minor partial demolition work usually requires specific heritage council approvals.
Partial house demolition generally requires planning permission when it involves:
- Demolition of load-bearing components
- Removal of street-facing façades
- Work on buildings in conservation areas
- Projects affecting the structural integrity of the building
Code of practice for full and partial demolition
The code of practice for demolition work provides essential guidance on managing health and safety risks. This approved code applies to anyone with a duty of care in demolition circumstances. Following these guidelines ensures compliance with workplace health and safety duties regarding demolition work.
Permit requirements and local regulations
Before any partial demolition project is started, written notification must be given to local regulators at least 5 days before work begins. This applies when:
- Demolishing a structure or load-bearing part at least 6 metres in height
- Using load-shifting machinery on a suspended floor
- Using explosives for demolition work
Documentation requirements often include site plans showing location details, descriptions of the building parts to be demolished, and information about protective measures. For partial demolition specifically, you’ll need calculations showing that the remaining structure will stay stable throughout the process.
Ensuring worker and public safety
Safety remains a top priority throughout every partial demolition project. All essential services must be disconnected according to the relevant authority requirements before any work begins. An expert must inspect sites for hazardous materials like asbestos, which must be removed before demolition commences.
Workers involved in demolition must also be fully trained and licensed. This training covers specific hazards associated with demolition work, ensuring everyone understands proper procedures and safety protocols before setting foot on site.
Key Takeaways
Partial building demolition might seem straightforward on paper, but as we’ve covered, there is a lot that must be considered and planned for before any work takes place.
From thorough structural assessments and navigating unexpected material challenges to choosing the right demolition methods and maintaining clear communication, success depends on expertise, precision, and attention to detail.
If you need a reliable demolition contractor in Southeast Queensland or the Sunshine Coast, Sellcon is the name you can trust. With over 16 years of industry experience, we specialise in delivering efficient, safe, and high-quality partial demolition solutions tailored specifically to your project’s needs. Partner with us to ensure your demolition is handled professionally from start to finish, keeping your property safe, compliant, and ready for what comes next.